
DESIGN AND ENGINEERING
DESIGN AND ENGINEERING
What is Design and Engineering?
Design and Engineering is one of the sub-branches of product development and is an interdisciplinary field of expertise that includes industrial design and mechanical design suitable for production.
​
Each of the areas of expertise such as Industrial Product Design, Plastic Part Design, Mechanism Design, Electronic Component Packaging Design are within Poligon Engineering's areas of expertise in design and engineering. You can follow the links for detailed information.
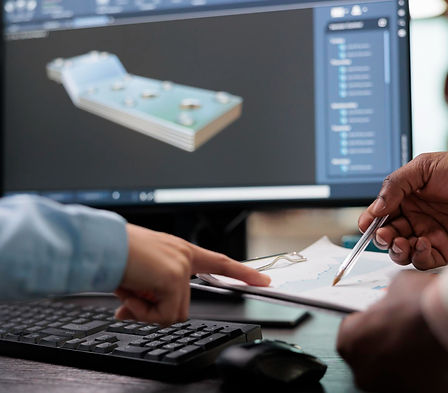

WASTE GROUP
REVERSE ENGINEERING
What is Reverse Engineering?
Reverse Engineering has different meanings depending on professional groups. For the manufacturing sector, it is the process of creating CAD data of a manufactured product using digitization systems. In other words, it is the discovery of engineering secrets.
How is Reverse Engineering Done?
For reverse engineering usually optical and laser scanner systems are used. First of all, polygon data of the part is obtained with the scanning system. Sections are taken from the obtained data using software. Sketches are created based on the sections taken. These drafts solids or surfaces is created and finalized. It can be done in a few different ways;
-
Parametric modeling can be done with Sketch-based modeling. Since solids and surfaces can be obtained from drafts, changes made through drafts are reflected in the entire design.
-
Data can be easily created by modeling with fast surface. Editing is done on the scan data. (such as closing gaps, cleaning deformations, arranging polygon numbers, smoothing or sharpening polygon transitions, etc.) Afterwards, the program automatically creates a surface on the polygon data.
The appropriate method is preferred based on part geometry, sensitivities, cost or application.
​
The difference between these two processes is that one is data obtained in a controlled manner and the other is data generated according to the software's own algorithm.
WASTE GROUP
SIMULATION AND ANALYSIS
What is Dynamic Analysis?
Dynamic stress can be obtained from experiment (sensor or mounting sensor on a physical component) or simulation.
Using simulation, a representative load history containing inertial forces and external forces (e.g., common reaction forces and torques) must first be created for accurate dynamic stress calculation.
Multi-body dynamic analysis methods that have typically been used for dynamic motion analysis can be used for dynamic load analysis of mechanical systems.
All bodies of the dynamic model are generally assumed to be rigid.
The rigid body assumption for a vehicle's suspension components generally yields reasonably accurate analysis results to support structural design for durability.


WASTE GROUP
What is Finite Element Analysis?
Finite element analysis (FEA) is an analysis method that measures and concludes how a product or a system will react to physical conditions such as force, impact, vibration, shock wave, heat resistance and liquid flow under current living conditions.
Finite element analysis shows whether the product has broken, worn out, or is not working as designed. This method is one of the key processes in the product development process.
FEA works by dividing a real object into a large number (hundreds of thousands) of finite elements (meshes), such as small cubes and prisms. This method examines the state of each mesh structure under physical conditions through mathematical equations.
The upper mathematical equations examine all these mesh structures holistically. Finite element analysis helps predict the behavior of products affected by many physical effects, including:
1. Mechanical stress
2. Mechanical vibration
3. Fatigue
4. Movement
5. Heat transfer
6. Liquid flow
7. Electrostatic
8. Plastic injection molding